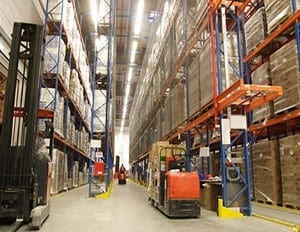
Every successful organization today, regardless of size, faces constant pressure to improve and adapt to changes in the business climate, customer preferences and available technology. This pressure to improve is especially obvious in areas directly impacting an organization’s bottom line, particularly the warehouse and distribution center. Demand for better WMS solutions to create efficiencies in these areas has resulted in a dizzying array of products ranging from embedded WMS modules that are included as part of an ERP solution and best of breed bolt-on WMS systems, to cloud-based systems that completely lack direct integration with business systems. ALSO SEE: 4 Signs Your Warehouse Needs a Barcoding System The warehousing and distribution sectors expend a lot of time and energy to fulfill their core missions: receiving, putaway, cycle counting, picking, lot control and inspection, replenishment, manifesting and shipping of inventory. They are established, conservative, and often seasonal business segments that have traditionally been driven by manual labor and disparate shipping and inventory tracking systems. Choosing the right WMS can not only make processes more efficient and help manage a workforce, it can also position an organization for growth and greatly improve customer service. But not all warehouse management solutions are created equal. If you’re tasked with looking for a WMS and are overwhelmed by the number of product choices and nuances, don’t throw your hands up and look to a crystal ball for answers. Instead, here’s a handy guide to the eight magic questions you need to ask yourself to ensure a WMS meets your company’s current and future needs. 1) How well do you know me? Does the WMS vendor thoroughly know who you are and specialize in the warehouse/distribution industry? If so, it will be able to help ensure that you are able to adopt industry best practices […]
Leave a Reply
You must be logged in to post a comment.