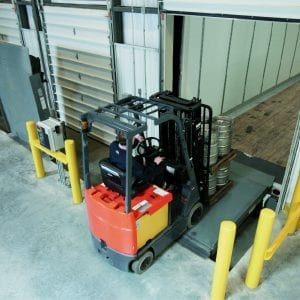
View original at www.plant.ca
All types of people work on the loading dock. Most tend to be younger, yet that’s where more aging Canadians are making a living. In fact, according to CARP (an association for retired people), individuals aged 55 years and older accounted for 36% of the working-age population, the highest proportion on record, and it’s expected to reach 40% by 2026, many of whom are in warehousing and distribution. But many facilities aren’t updating their loading dock equipment in the same way they’re doing so inside the plant. Robotics, AS/RS systems, AGVs and warehouse management systems are rapidly taking Canadian plants into the 21st century, while they continue to use manual – and potentially dangerous – procedures on the loading dock. Thanks to newer technologies such as automatic vehicle restraints and push-button hydraulic levellers with smooth transition features, these practices no longer need to be backbreaking – especially for aging workers. Forty years ago, manually securing trailers to a loading dock bay would require workers to go outside, regardless of weather and environment, and physically set wheel chocks on a trailer’s rear tires. Some facilities still use this risky method, placing employees on the busy drive approach with the most basic form of vehicle restraint. These types of manual operations are not only time intensive, but potentially dangerous. The US Occupational Safety and Health Administration (OSHA) – frequently cited in Canada – recently reported that tractor-trailers are the second leading cause of back-over deaths. Safer operation Internationally, recommendations are also being made to keep valued employees off the dangerous drive approach with the help of semi back-up alarms (New Zealand) and bumper refuge zones (France). With today’s technology and changing standards, there’s little to no reason for employees to chock tires outside. Automatic restraints lock onto the trailer’s wheels or […]
Leave a Reply
You must be logged in to post a comment.