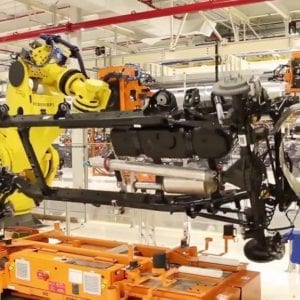
View original at www.automationworld.com
Asynchronously indexing AGV assembly line. We’ve installed more assembly-line automated guided vehicles (AGVs) for manufacturers in the past few years than ever before. The global economy is rapidly changing and we’re seeing a strong demand for manufacturing solutions that can respond quickly to those changes. Many customers don’t know what questions to ask or what technologies might be options or what solutions to apply. AGVs are a perfect fit for assembly lines and material handling where you need 24/7 operation, onboard power for lift or rotation, high duty cycles or heavy payload transport. So how do you know if AGVs are a fit for you plant? Do you need flexible paths and processes? Traditional conveyance doesn’t offer flexibility in paths, processes or products. With pits, chains and metal tracks, it is dirty, noisy and expensive to change out. It doesn’t allow manufacturers flexibility to make changes in an environment that must be able to do so. Whether through inductive power transfer, magnetic tape or geolocation, AGV paths can be quickly changed. There are typically few monuments involved, even for very heavy and complex products. If the AGVs have an onboard programmable logic controller (PLC), they can be reprogrammed to respond to process changes by spending less time in station, advancing asynchronously, requiring process completion for advancement, and more. Do you want to be able to scale as you go? Product launches often entail some type of ramp-up, with limited initial production preceding full throughput rates. With traditional chain-based conveyance, manufacturers essentially have to buy all the conveyance they’ll ever need, before they really need it. It’s generally not practical to install part of an overhead power and free track, or just a few skillets. Instead, they have to make the full conveyance investment at the start of the project, […]
Leave a Reply
You must be logged in to post a comment.